In the realm of chemical processing, the importance of robust and reliable equipment cannot be overstated. Among the essential components, the stainless steel reactor vessel stands as a workhorse, playing a pivotal role in a myriad of applications. Whether it’s the pharmaceutical industry, petrochemical plants, or food processing, these vessels offer a safe and efficient environment for various chemical reactions. This article delves into the features, advantages, applications, and other aspects of the stainless steel reactor vessel, highlighting its significance in modern industrial processes.
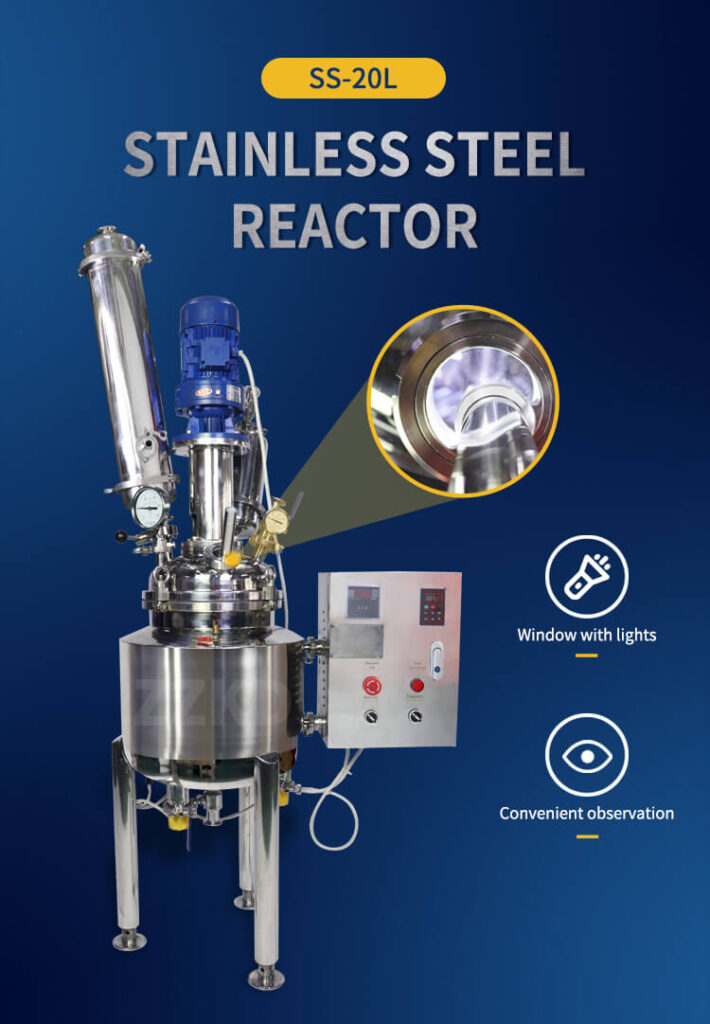
Features of Stainless Steel Reactor Vessel
The stainless steel reactor vessel is designed with several key features that make it an ideal choice for chemical processing applications:
1. Material Strength: Stainless steel, with its excellent mechanical properties, provides high strength and durability to the vessel, ensuring it can withstand varying pressure and temperature conditions.
2. Corrosion Resistance: One of the standout properties of stainless steel is its corrosion resistance. This resistance to chemical reactions makes the reactor vessel suitable for handling corrosive substances without compromising the material integrity.
3. Hygienic Properties: Stainless steel possesses inherent hygienic properties, making it suitable for applications in the pharmaceutical and food processing industries, where maintaining the purity of the final product is critical.
4. Temperature Control: The reactor vessel is equipped with advanced temperature control mechanisms, allowing precise regulation of the reaction environment. This feature is crucial for achieving desired reaction rates and product yields.
5. Pressure Regulation: With pressure safety valves and control systems, stainless steel reactor vessels can operate at both high and low pressures, ensuring the safety of the process and the operators.
6. Ease of Cleaning: Stainless steel surfaces are smooth and easy to clean, reducing the risk of contamination during product changeovers or when transitioning between different reactions.
7. Versatility: The reactor vessel can accommodate a wide range of chemical reactions, making it a versatile asset in various industries.
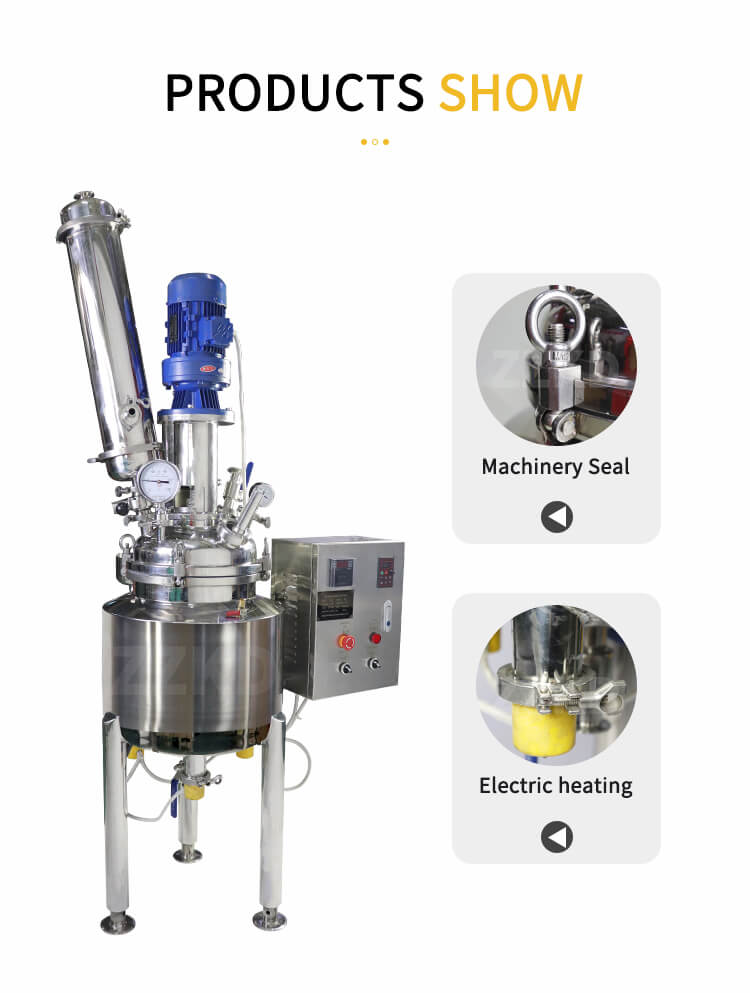
Advantages of Stainless Steel Reactor Vessel
1. Enhanced Safety: The use of stainless steel ensures a safe operating environment due to its ability to resist corrosion and handle high-pressure conditions. This significantly reduces the risk of accidents and potential hazards associated with chemical reactions.
2. Longevity and Reliability: Stainless steel’s durability and resistance to wear and tear contribute to the longevity and reliability of the reactor vessel. This leads to reduced maintenance costs and increased operational uptime.
3. Ease of Customization: Stainless steel reactor vessels can be custom-designed to suit specific process requirements. This flexibility allows industries to optimize their chemical processes and achieve higher productivity.
4. Regulatory Compliance: Many industries, such as pharmaceuticals and food processing, have strict regulatory requirements. Stainless steel reactor vessels often meet these standards, facilitating compliance with health and safety regulations.
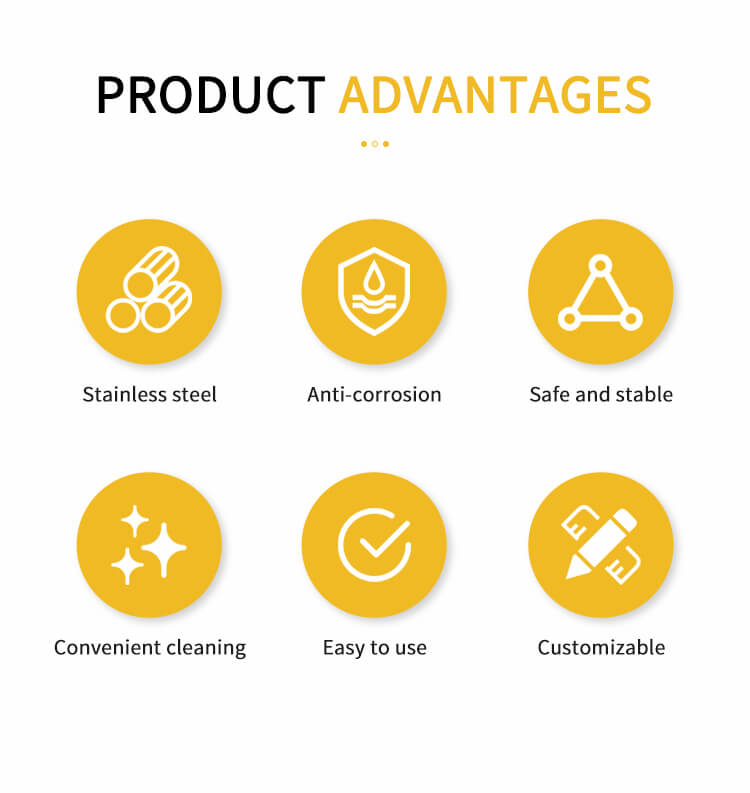
5. Cost-Effectiveness: Although stainless steel reactor vessels may have higher initial costs compared to some other materials, their long lifespan and low maintenance needs make them cost-effective in the long run.
6. Environmental Friendliness: Stainless steel is a fully recyclable material, aligning with sustainable practices and reducing the environmental impact of industrial processes.
Applications of Stainless Steel Reactor Vessel
The applications of stainless steel reactor vessels are diverse and widespread across multiple industries, including:
1. Chemical Industry: Reactor vessels are extensively used for chemical synthesis, polymerization, and blending processes.
2. Pharmaceutical Industry: These vessels play a crucial role in pharmaceutical manufacturing, including the production of drugs, vaccines, and various pharmaceutical intermediates.
3. Petrochemical Plants: Stainless steel reactor vessels are employed in refining processes, such as catalytic cracking and hydrocracking, to produce fuels and petrochemical products.
4. Food Processing: In the food industry, reactor vessels are used for processes like fermentation, enzymatic reactions, and food preservation.
5. Cosmetics and Personal Care: Reactor vessels are utilized to produce cosmetics, toiletries, and personal care products.
6. Adhesives and Resins: The production of adhesives, coatings, and resins also relies on the use of stainless steel reactor vessels.
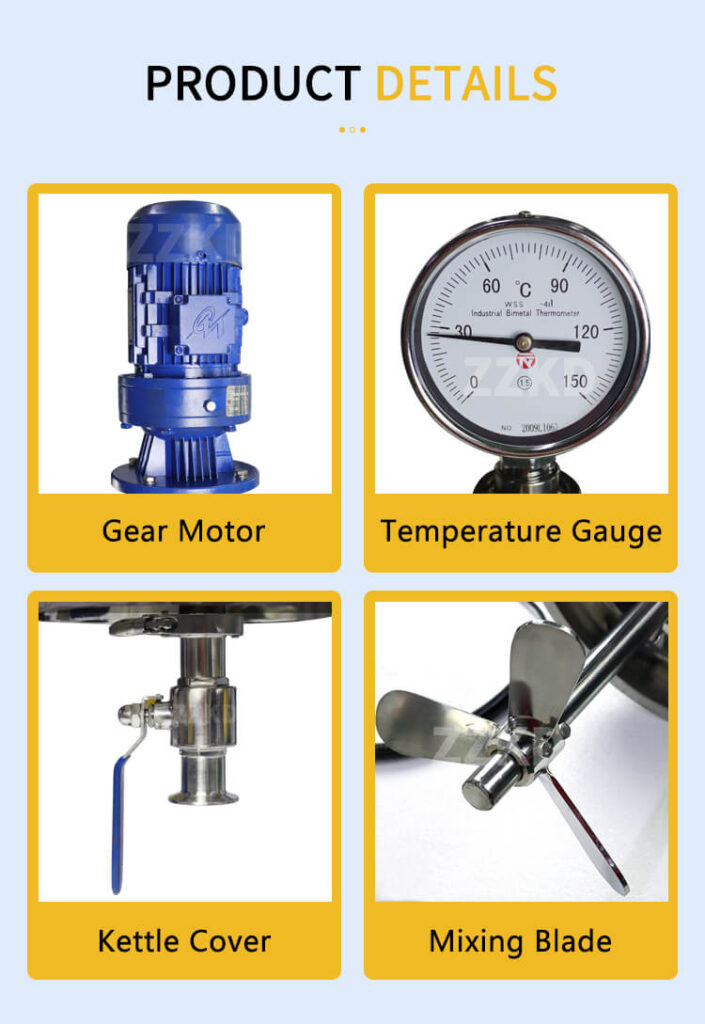
Case: Stainless Steel Reactor Vessel in Pharmaceutical Industry
A prominent pharmaceutical company faced a challenge in scaling up the production of a life-saving drug. The chemical reaction involved was highly sensitive to temperature and pressure fluctuations. The company opted for a stainless steel reactor vessel due to its superior heat transfer capabilities and resistance to corrosion from the reactive chemicals involved.
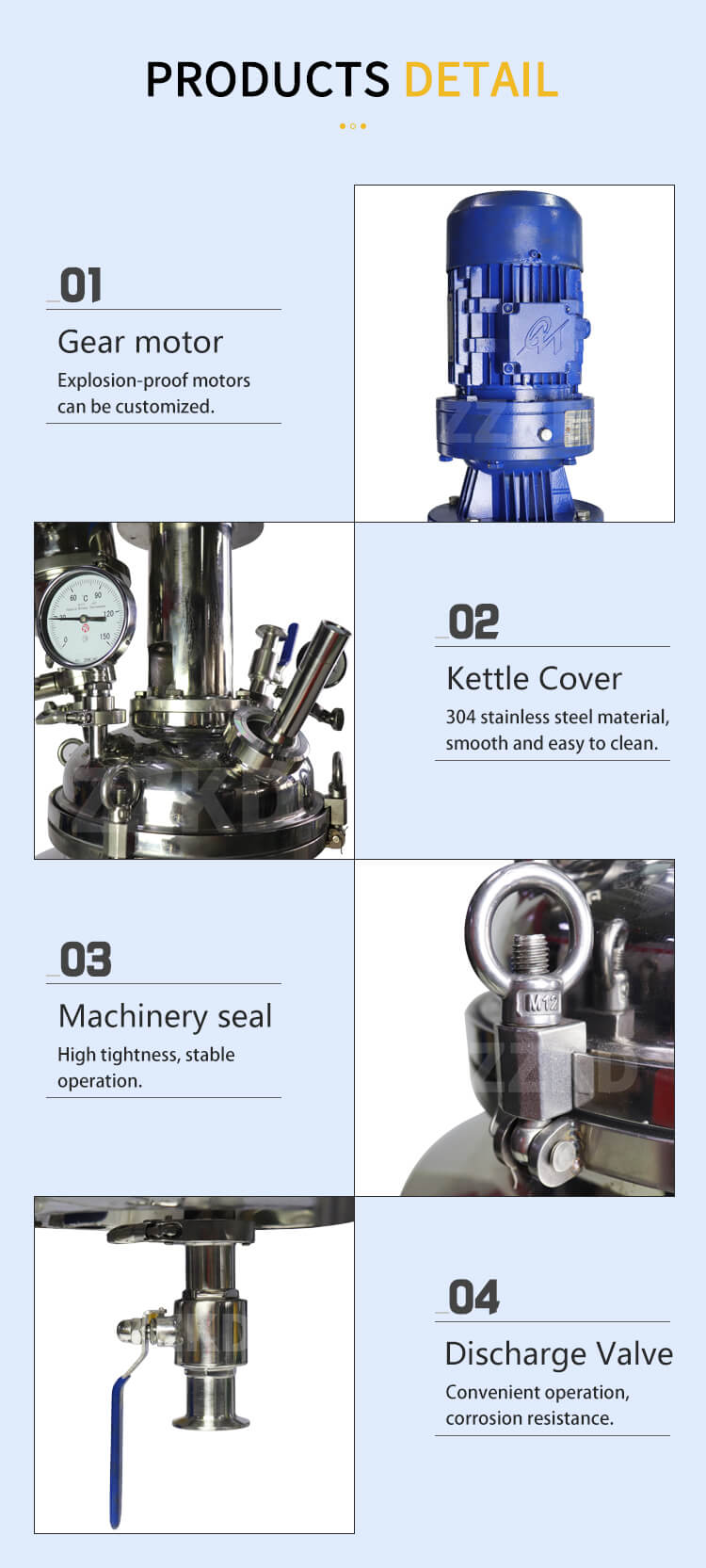
The result was outstanding – the company successfully increased production volumes while maintaining consistent product quality and purity. The stainless steel reactor vessel’s precise temperature control and pressure regulation capabilities ensured that the reaction proceeded smoothly and safely, eliminating the risk of costly batch failures. Additionally, the vessel’s hygienic properties allowed for seamless cleaning and ensured compliance with stringent pharmaceutical industry standards.
Conclusion
The stainless steel reactor vessel is an indispensable asset in chemical processing, providing a safe, reliable, and versatile solution for various industries. Its robust construction, corrosion resistance, and temperature control features make it an ideal choice for critical reactions in pharmaceuticals, petrochemicals, food processing, and other sectors. As technology advances, we can expect further refinements in stainless steel reactor vessel design, enabling more efficient and sustainable chemical processing in the future.