Chemical glass batch reactors, particularly the 10l jacketed glass reactor, are essential in various laboratory and industrial processes. These reactors are pivotal in conducting chemical reactions under controlled conditions. The design of a chemical glass batch reactor allows for precise control over reaction variables such as temperature, pressure, and mixing speed, ensuring accurate and repeatable results.
This type of reactor is especially useful for reactions that require specific temperature conditions, as the jacketed design allows for both heating and cooling of the reaction mixture. The 10l capacity is ideal for small to medium-scale experiments, making it a popular choice in research and development labs.
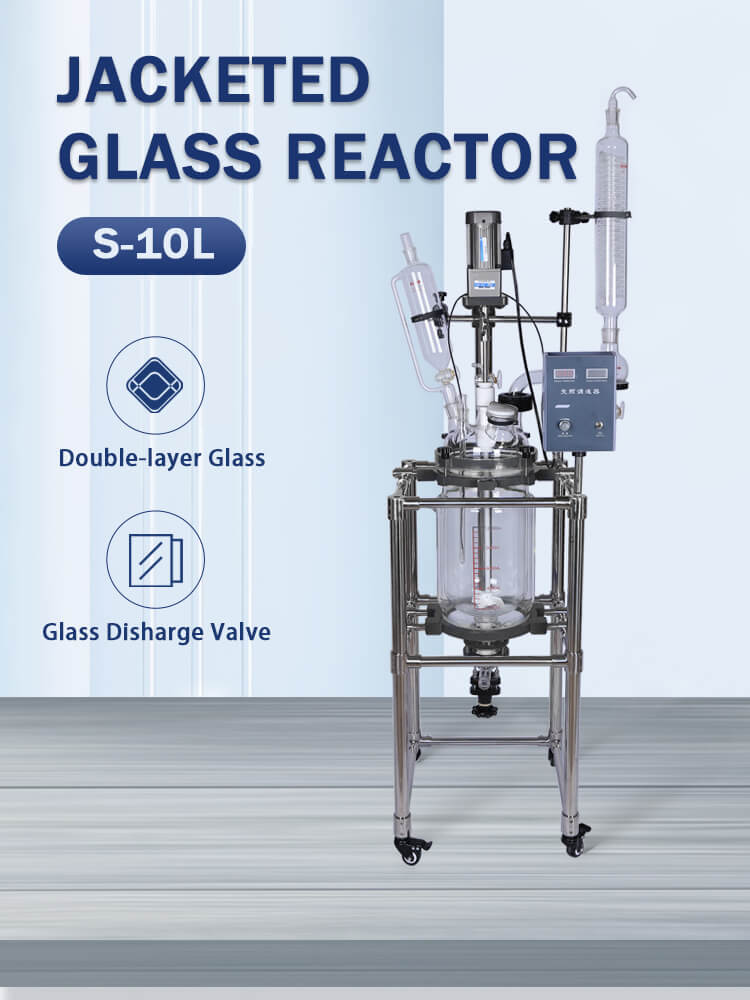
Key Features of Chemical Glass Batch Reactors
Chemical glass batch reactors are renowned for their durability and chemical resistance. Made from high-quality borosilicate glass, these reactors can withstand harsh chemicals and high temperatures without compromising structural integrity. This resistance is crucial for experiments involving corrosive substances or extreme conditions.
Another significant feature is the clarity of the glass. This transparency allows researchers to visually monitor the reaction process, which is vital for understanding and controlling the reaction kinetics.
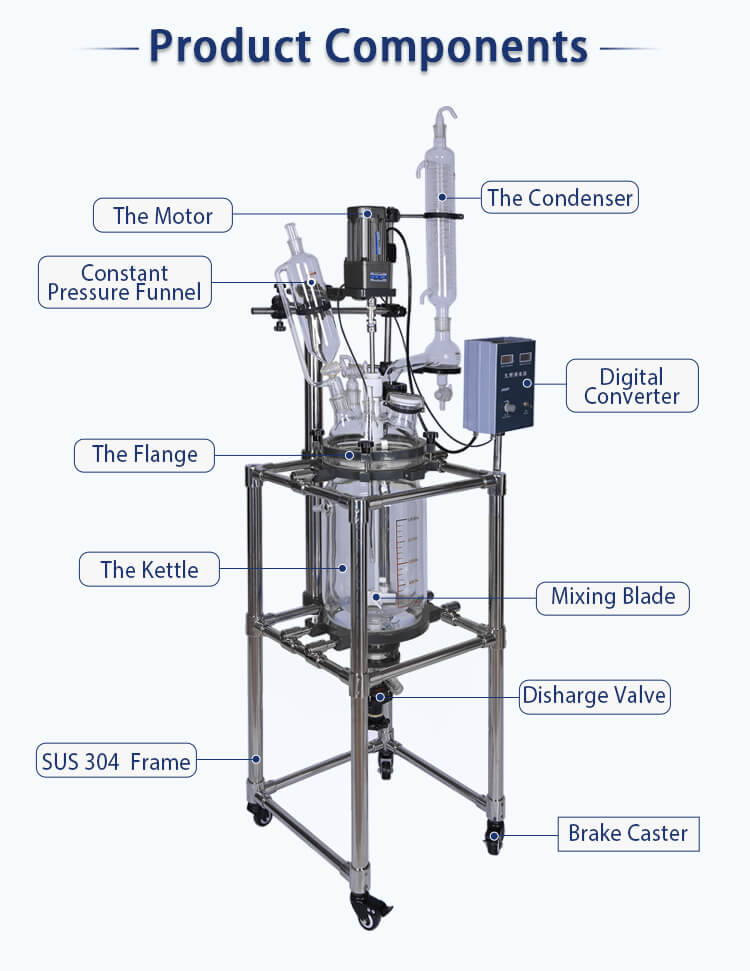
Advantages of Using a Glass Reactor
The use of a chemical glass batch reactor brings several advantages. Firstly, the inert nature of glass ensures that there is no interaction between the reactor’s material and the chemicals inside, thus preventing contamination. Secondly, the ease of cleaning and maintenance of glass reactors enhances their longevity and reliability in a laboratory setting.
Moreover, the transparent nature of these reactors provides an unobstructed view of the contents, facilitating better observation and analysis of the reaction process. This transparency is particularly beneficial in educational settings where students can visually learn about reaction dynamics.
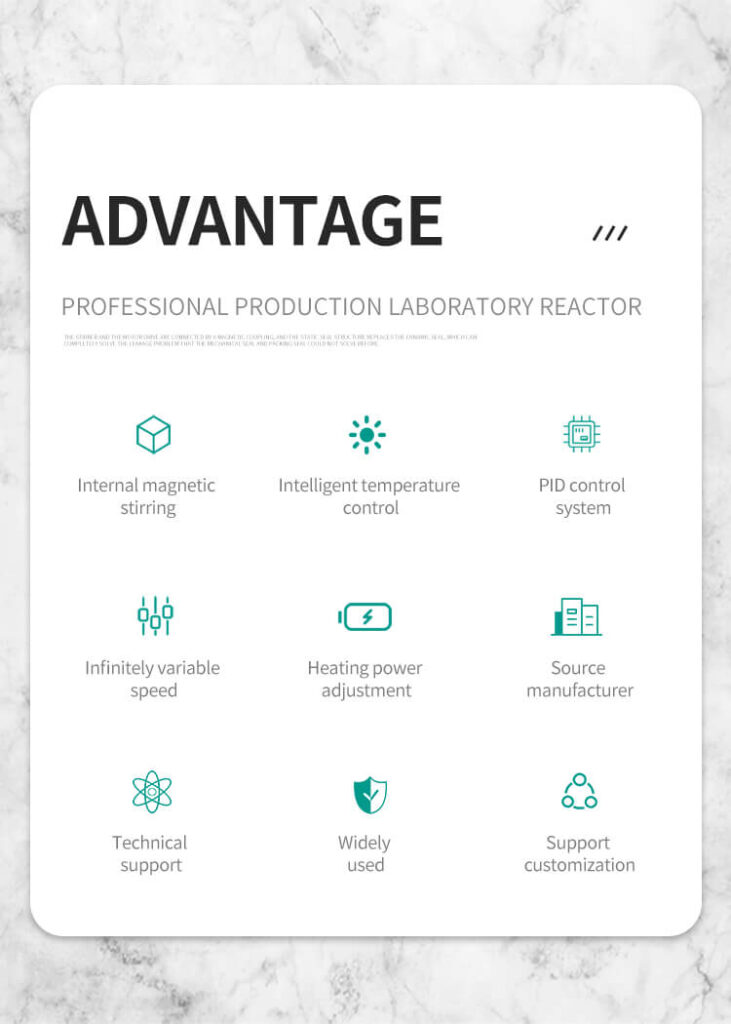
Applications in Various Industries
Chemical glass batch reactors find extensive applications across multiple industries. In the pharmaceutical industry, they are used for drug development and testing. Chemical companies utilize these reactors for pilot plant and scale-up studies. Moreover, they are instrumental in academic research, providing a reliable platform for conducting controlled chemical reactions.
The adaptability of these reactors to different scales of operation makes them versatile tools in both small-scale laboratory experiments and larger industrial processes.
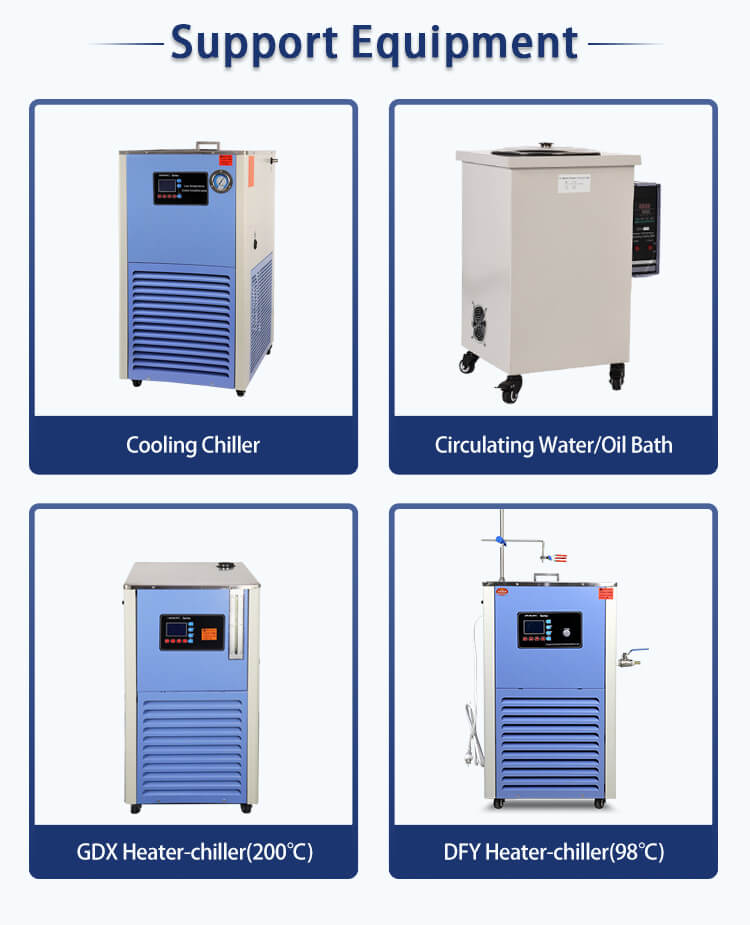
Technological Innovations in Reactor Design
Technological advancements have significantly enhanced the functionality of chemical glass batch reactors. Innovations include automated control systems for precise regulation of reaction parameters, advanced stirring mechanisms for better homogeneity, and safety features like pressure relief systems.
These technological improvements not only increase the efficiency of the reactors but also enhance safety, a critical aspect when dealing with hazardous chemicals.
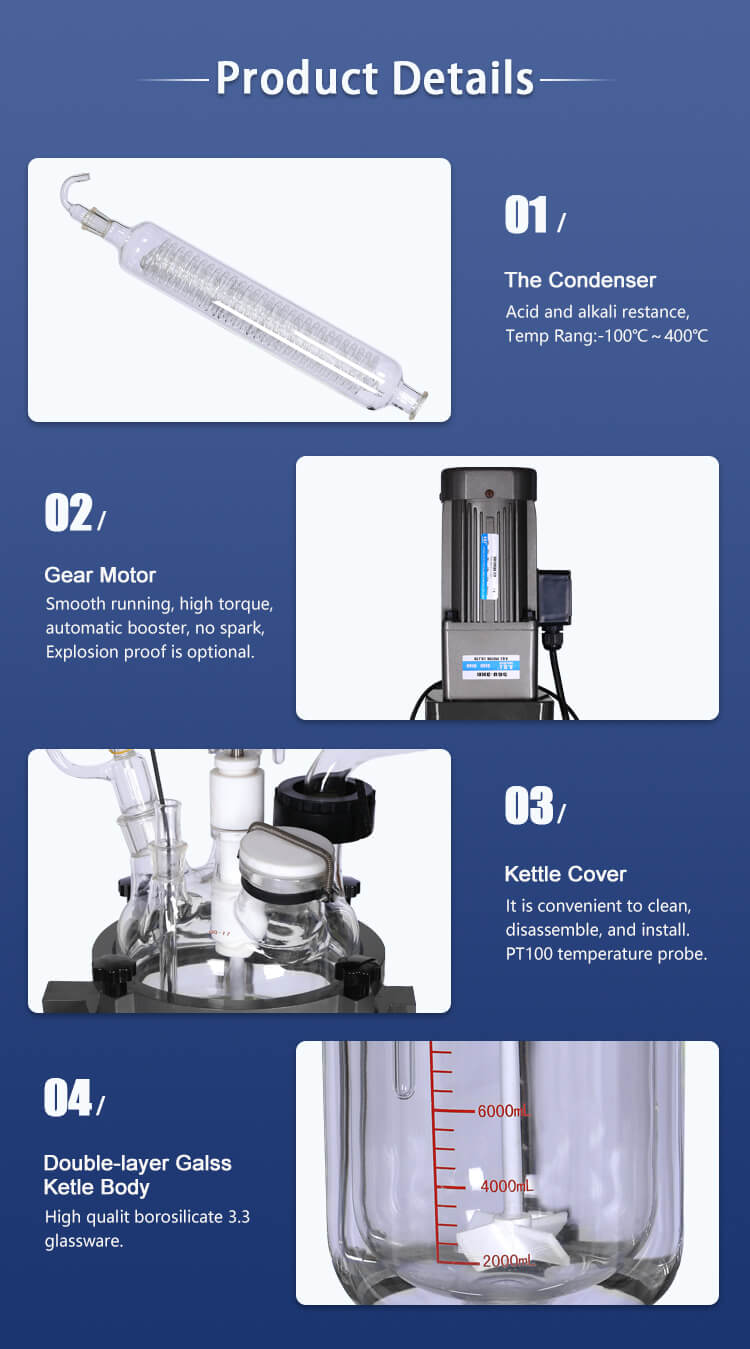
Choosing the Right Reactor for Your Needs
Selecting the appropriate chemical glass batch reactor for specific applications is crucial. Factors to consider include the volume of the reactor, type of jacket for temperature control, and the compatibility of the reactor with the chemicals involved. For small to medium-scale reactions, a 10l jacketed glass reactor often serves as the ideal choice, offering both versatility and efficiency.
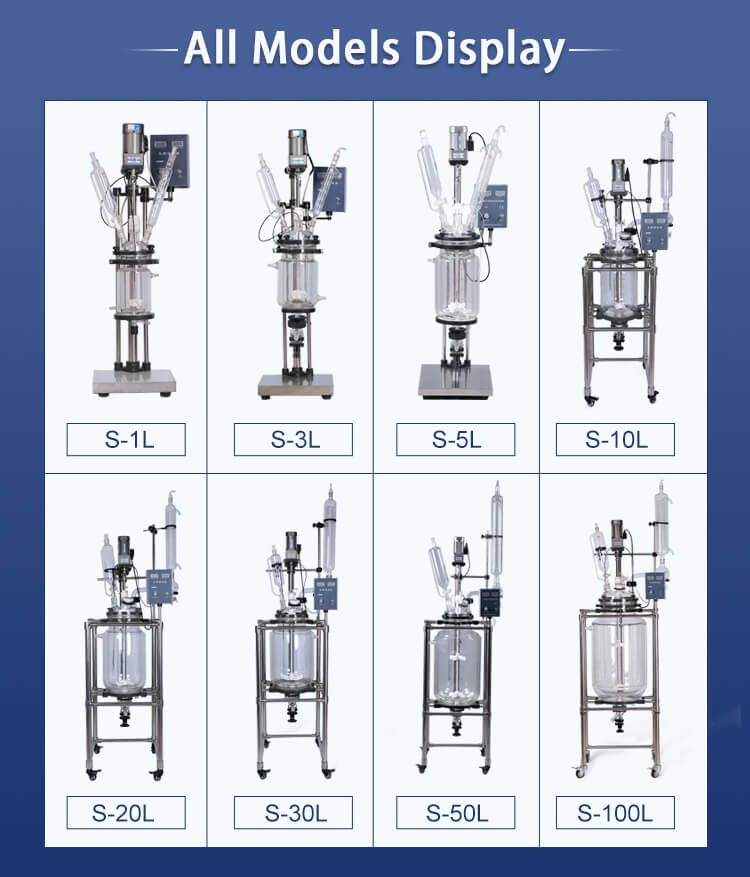
Conclusion: Partnering with FBL Machinery and Instrument Equipment Co., Ltd.
In conclusion, chemical glass batch reactors, especially the 10l jacketed glass reactor, are indispensable tools in the realm of chemical research and industrial processes. For those seeking high-quality reactors, FBL Machinery and Instrument Equipment Co., Ltd. offers a range of products that are not only efficient and reliable but also tailored to meet specific customer needs.
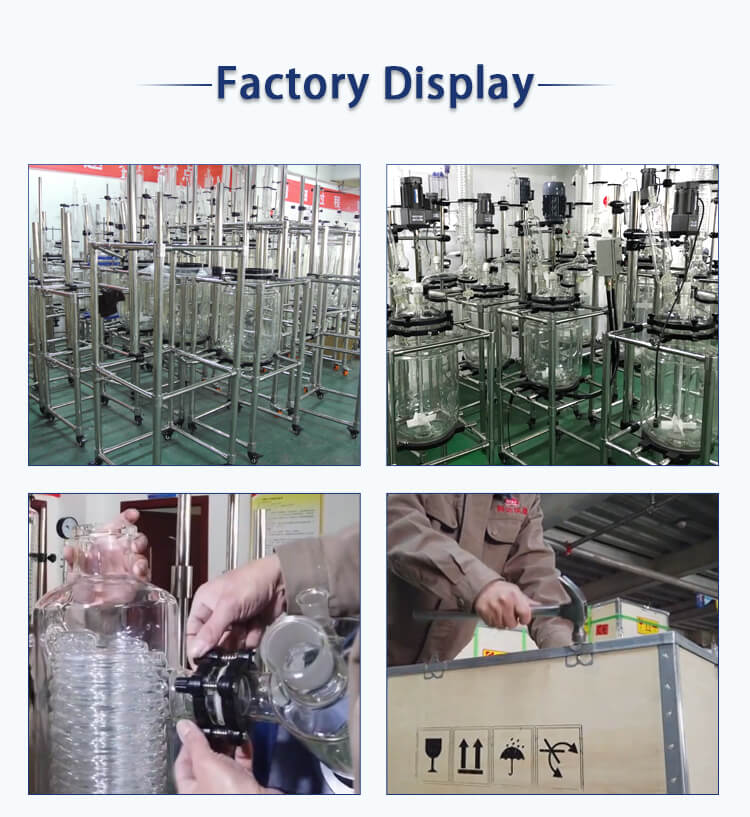
Visit FBL’s website to explore their comprehensive range of reactors and find the perfect solution for your chemical processing needs. Remember, choosing the right reactor is not just about meeting current requirements, but also about ensuring reliability and efficiency for future projects.